Custom Made For Your Welding
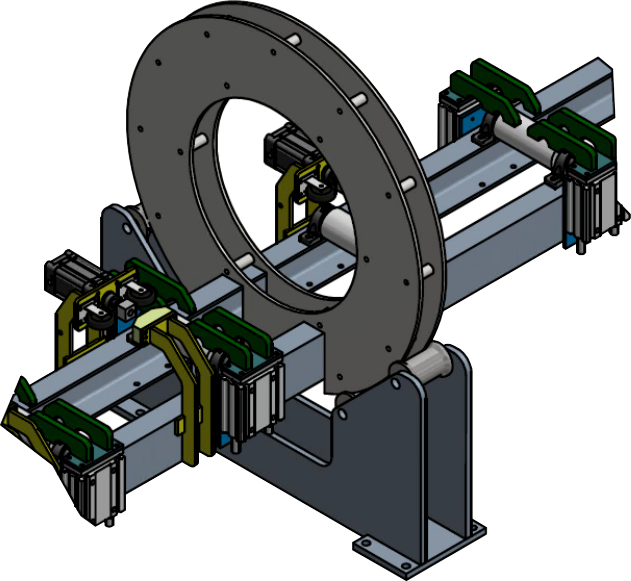
R&E Engineering provides custom welding jigs to be used in conjunction to our supplied welding positioners. Every welding jig is designed according to your product specifications and welding requirements. We make sure that the design allows high accessibility for both the welding robot and the operator, is user-friendly and cost-effective.
The welding jigs are separate to the robotic welding positioners. They are attached to the face of the welding positioners enabling synchronised movements with the welding robot and allowing the workpiece to be moved and rotated to provide the robotic welding system with utmost accessibility.
Welding jigs can would have either pneumatic or manual welding clamps, depending on the client’s preferences. Clamps are positioned on the welding jig for accessibility and ease of use, whilst keeping the workpiece securely attached for the welding process.
Please see below for some examples of our custom welding jigs. Our designs are not limited to the examples below. We can custom design a welding jig for any type of welding process and workpiece.
Don’t wait any longer! Enquire here and find out what we can do for you!
T-Bar Welding Jig
The T-Bar Welding Jig would be attached to a rotating welding positioners and works using pneumatic clamps to secure the workpieces. This set up requires a crane for workpiece placements.
Once everything is secured, the welding robot will move synchronously with the welding positioners, giving welding access to every nook and cranny of the workpiece. Ensuring perfect welds, every time.
I-Beam Welding Jig
This I-Beam Welding Jig is specially made for an extra-long I-Beam weld. The metal plates for the I-Beam are clamped using pneumatic clamps which sits the workpiece on a gravity roller.
When the welding process starts, the welding robot welds along the welding jig. Once it is finished on one side, the welding positioners spins, turning the welding jig and workpiece around, providing access for the welding robot. Once everything is done, the welding positioner spins back to its default position and clamps releases. The I-Beam then can be pushed along the roller to an output station.